"
Standardization" is a
critical factor that is constantly overlooked because of inadequate management, project planning, sense of urgency (it takes too long), geographic locations and poor communication mediums.
Business Companies, Educational Instituitions and Governmental Agencies are constatly laying out plans (well some do) to scale back in one way or another. They often do this with no idea that people coming (cheaper wage) in or now doing more than one job must have standardized methods and procedures, work tasks, job aides and up to date manuals to do a job correctly. If not, you are just cutting your throat deeper.
The only time I saw a company try and get standard work procedures was before a strike so that management could keep operations running smoothly. At the same time, union employees were hiding work tasks or bringing out outdated procedures.
The problem is not just in Business one,
Governmental and Educational Systems have no idea when they continuously develop and delegate down new procedures, targets and measurements based on some new expert or governmental (i.e., No Child Left Behind, State educational tests and improvement programs) mandate that changes when new people are elected to government or school boards.
One of the main problems is no one/agency removes the previous mess because they don’t want to be associated with a failed plan or they just don’t understand it, their new ideas will fix the problem and they will have it done during their term in office.
Sub-optimization is rampant in our business, governmental and educational systems. It’s everyone/agency doing their best, but they have no idea where to start. I suggest Standardization. You must get control of your system before any improvement can take place. Designing new systems/processes that contradict current or previuos ones will result in failure.
The following write-up is on Standardization, why it is important and what key elements make up Standardization.
My experience with Process Improvement Teams has proven there can be no long-term effective improvement without standards. Standardization is the starting point and the ending point for continual improvement.
Dr. Nakumura a leading expert on Standardization stated:
" If you simply implement standardization without first making improvements, you will only establish more firmly the problems that exist in the current system. The correct approach to standardization begins with setting a course for higher levels of operations and standardizing improved methods rather than current methods.
Standards are not meant to last forever... standardization should be optimistic: there is always room for improvement. Perfect standards do not exist at any company."
Shigehiro Nakumura
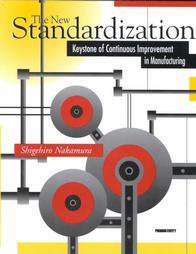
Based on this information and my experiences I would define Standardization as follows:
Standardization is a disciplined process that maintains the gains as well as provides a means for continual process improvement by applying methods, measurements (stability, capability), and procedures in a systematic fashion that prevent a process from reverting to old ways and root cause from reoccurring.
Simply stated "standardization" is making sure that the good effects of our systems are not lost through neglect, forgetfulness or organization changes. Standardization/Empowerment without parameters equal CHAOS!
Why then is Standardization important? Quality/Process training has taught us that many of our current processes, and especially those that have been in place for a while have probably deteriorated over time. There is little doubt that everyone is working hard and doing what they think is right, but in many cases there is no clear sense of direction, or the knowledge or understanding of what is driving the complete process, let alone one's own piece of the process.
CLICK PIC TO ENLARGE PICTURE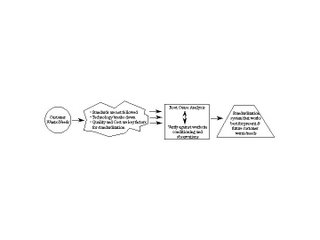
Standardization helps employees (i.e., teachers) and work groups drive in the same direction and toward the same goals, which is vital to exceeding customer expectations and student success. Benefits of standardization include:
• Educating employees (i.e., administrators) in identifying their customer
and supplier expectations
• Providing up to date documentation, standards and procedures created by employees/teachers who do the work
• Reducing rework
• Creating proactive vs. reactive opportunities for improvement by assuring stability and capability
• Identifying and clarifying critical processes based on customer/educational expectations
• Enabling better coordination among work groups within the organization
• Promoting systematic identification and removal of root causes that inhibit process improvement
• Assuring decision making is based on facts and subject matter expertise
that is required for making sound decisions about redesign and implementation
• Guarantees achievement of Process Improvement in less time, and with less rework, that provides lasting results
Basically there are four major elements that are required for Standardization to take place:
1) Develop a Strategic Plan that Analyzes and Prioritizes critical processes for Standardization. Remember, you don't have to Standardize the total process, look for sub-processes most in need based on customer wants/needs.
TOOLS/TECHNIQUES: Strategic Plan (Hoshin)
Five Ws (Who, What, When, Where Why) and One H (How)
Standards Procedure Checklist (see below)
2) Lack of Communication is one of the main reasons for confusion and neglect when new standards are introduced. Everyone must own and operate within the process. This is especially true when trial implementations are in effect. If one district, (location) department or center is doing things by the new method and another department, district or center is doing things by the old, communication is the key to measure the result.
3) Adequate and continual Training and Education must be done in order for standards to be effective. No matter how good the standards, procedures, measurements and methods look on paper they will not benefit the employee/teacher, employer/administrators and most importantly the customer/student unless all the critical parties are involved in the process from end-to-end are covered. Remember, most people learn their work by seeing and doing, not by reading big manuals or countless Emails and Handouts.
4) Accountability and Responsibility are crucial to Standardization. Evidence has repeatedly shown that problems will initially be solved only for the same problem to reoccur later. The major cause of this is that standards were observed at first, but eventually were allowed to deteriorate because of lack of discipline. A system of responsibility must be set up to assure that PDSA (Plan, Do, Study, Act – Shewhart & Deming) continue to happen on each critical process.
Without proper standardization there is a constant need for management/supervision to instruct, watch, inspect and monitor the work process very closely. Instead we must create a standardization process that is both customer focused and employee-oriented. By changing the perspective of our process improvement efforts from tasks and procedures to customer outcomes, and by putting the process directly into the hands of the workers/teachers rather than rocket scientist documentation, we can create a definition of value added activity that guides employees to continuous process improvement. Oh yeah, keep politicians out of the process!
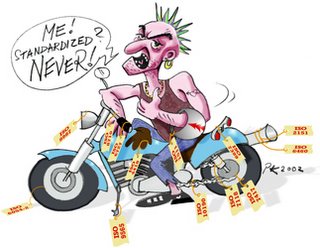
STANDARDIZED PROCEDURES CHECKLIST
The following procedural checklist provides the basic steps for a Process Team or Work Group to standardize strategic work processes:
1) Define and Identify Critical Work Processes that are in accordance with corporate strategies and goals.
2) Of these, prioritize which work processes do not consistently meet customers’ needs and expectations and select a Top Priority Process by evaluating:
• Impact on Customer (Ext/Int)
• Impact on Business
• Need to Improve
3) Select appropriate employees (work group) doing the job as well as those supplier support functions (i.e.; M&P, IT, Sales, Marketing, Training, Operations) to describe the work process and gather existing:
• Job Aids
• Procedures/Work Flows
• Standards/Manauals
• Checklists
• Job Descriptions
• Training Documentation
• System Code (if applicable)
4a) Develop process flowcharts reflecting how work is currently being done.
• Determine if workflow and employee practices are consistent with existing Procedures, Standards, Job Aids, Checklists, Training Documentation, Work Flows and Job Descriptions.
• Determine degree of consistency of employee practices within the work group through observations and interviews or Quality System Assessments.
4b) Identify Suppliers (INT/EXT) and your expectations of them (Inputs).
Identify Customer (INT/EXT) expectation (Outputs). Use SIPOC Model.
4c) Select best workflow and employee practices based on group consensus. Document new Procedures and Standards to reflect changes.
5) Develop upstream Process and outcome Result (Quality) Indicators. These indicators should be based on customer expectations and be:
• Measurable
• Verifiable
• Cost Effective
• Tamper Proof
Use indicators to determine baseline performance.
6) Systematically collect data (indicators) to determine on-going performance. Analyze process performance; determine if work process consistently meets customer expectations.
• Process is Stable
• Process is Capable
Note --> Remember that a process can be stable but not capable. Stable does NOT always mean good.
7) As opportunities arise through end-to-end analysis and performance indicators, implement and verify solutions (downstream effects). Standardize across work groups. If problem s are more complex and requires further analysis establish a Process Improvement Team.
8) Determine Process Flexibility, if work process cannot be improved (i.e.; ECRS methodology) to meet current or "anticipated future" customer/student expectations consider total redesign of the work process.
• E = Eliminate
• C = Change/Add
• R = Rearrange
• S = Simplify
Continuously share work process innovations, lessons learned and new procedures with appropriate work groups (i.e., suppliers/parents, internal customers/teachers, similar functional groups). Consider these elements:
• Methods & Procedures updated
• Simplification - measure essential indicators only
• Train employees actually doing the job
Note --> This is critical if you are losing experienced employees because of downsizing, early retitements, and buyouts. The graph below expalins this scenario.
CLICK PIC TO ENLARGE PICTURE
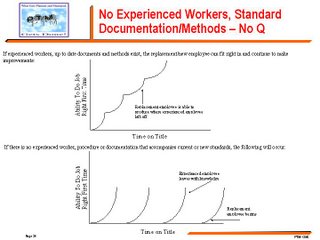
Note: --> Do not get fooled into thinking the Internet has solved this problem. The Internet only speeds up the process, it does not know if something is Standard or not, it still comes down to people.
How about the importance of Standardization in Education?
According to a new report on statewide testing released today by the American Federation of Teachers (AFT), most states have made progress in developing clear grade-by-grade standards, but many have not aligned their high-stakes math, reading and science tests with a strong set of content standards, which leads to a distorted picture of how students, schools and teachers are performing.